Summary
The Faculty of Science and Technology has successfully led a joint submission with the Faculty of Media and Communication and the Business School that is being supported by the March 2021 call for ‘game-changing’ research concepts to enable growth of BU2025 Strategic Investment Areas (SIAs).
We are very excited that, through our existing state-of-the-art advanced materials and manufacturing facilities at the Design and Engineering Innovation Centre, BU now reunites all the conditions required to becoming World-leader in ultrasonic fatigue testing of advanced materials. Our wish is that this will ultimately impact in the World’s eco-economy and sustainable development.
Our Mission
Having as primary SIA Sustainability, Low Carbon Technology & Materials Science, the ADDISONIC (Advanced Manufacturing Ultrasonic Fatigue Prediction and Life Extension) mission is to contribute to reducing global waste by extending the life and enhancing the optimisation of any engineered systems through incorporating novel advanced materials tested under ultrasonic fatigue for quick and reliable predictability of properties to extend their lives. Therefore, the project addresses the UN sustainability goals of Industry, Innovation and Infrastructure; Responsible Production and Consumption; and, Climate Action.
The project also aims at contributing to fostering networking between BU and local or national businesses and industries, whether in this research area or in any other field where BU academics have strengths.
What industries partnering up with us will find
Making use of the Design and Engineering Innovation Centre at Bournemouth University, our partners will find cutting-edge laboratories and workshops featuring industry-standard facilities and the latest rapid 3D printing, prototyping, and manufacturing equipment. We also have long-lasting collaborations with other UK-based and international Universities to access additional expertise, such as the University of Hertfordshire or the University of Lisbon.
Why is this research a priority?
With up to 4x lower scrap material generated in parts manufactured, metal additive manufacturing is more eco-friendly. The market is estimated to grow by £4.42bn between 2016 and 2024 with an annual growth rate of 14%. However, little is known about the lifetime properties of novel advanced materials, such as metal additive manufactured ones. Knowing that approximately 90% of all metallic failures are due to cyclic loadings, we will lead global research into the application of ultrasonics for fatigue testing of advanced materials as it is the only method to quickly determine the predictability of material properties that will be subjected to cyclic loading. Ultrasonic fatigue testing machines enable tests to be extended to 1 billion cycles in just a few days compared to months or years (figure 1), which has as growth driver the adoption of “just-in-time” processes.
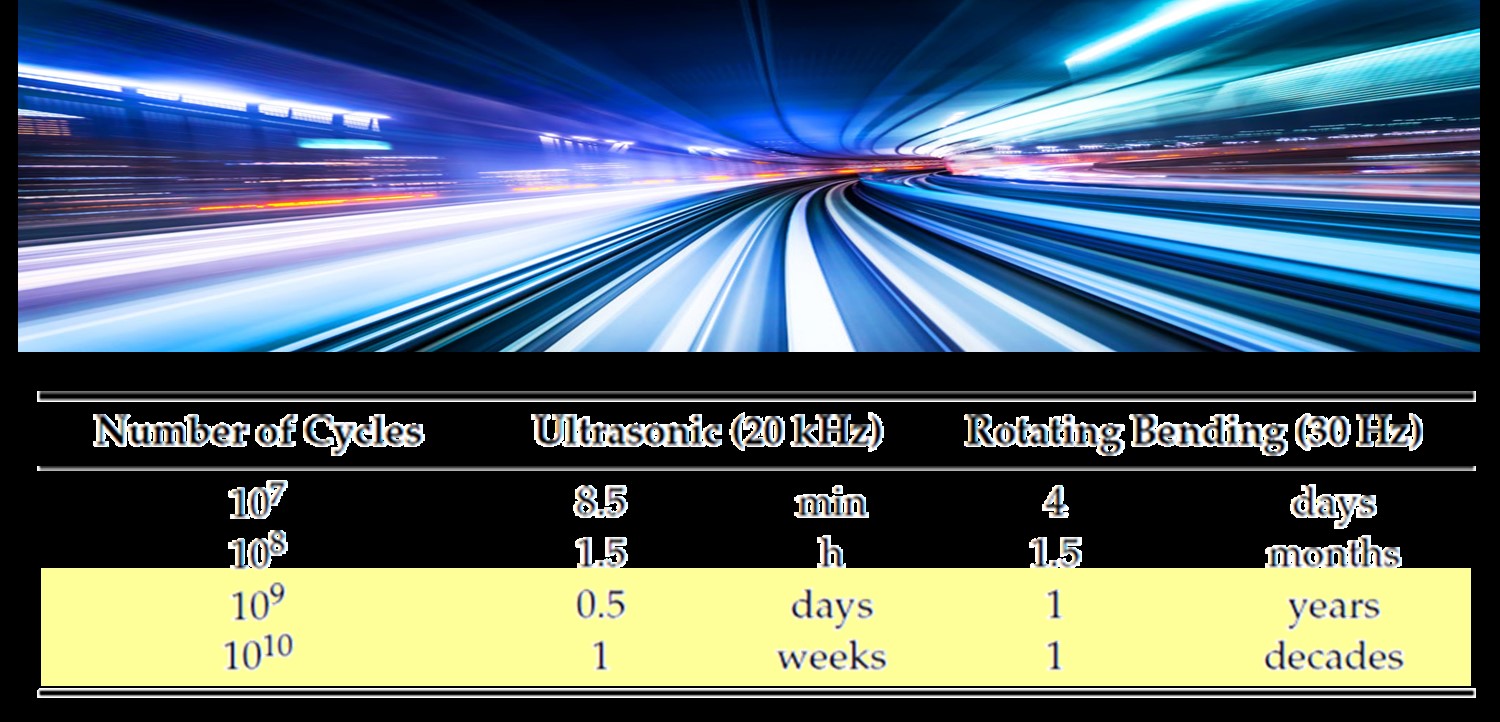
Figure 1. Comparison between the duration different fatigue testing methods need to be completed, assuming tests can run uninterruptedly.
Furthermore, recent developments show it is possible to carry multiaxial testing too, including with different biaxiality ratios. The PI, Dr Diogo Montalvão, was the first researcher in the World to adapt specimens being loaded in two directions (known as ‘cruciform biaxial specimens’) to ultrasonics. This is important because most fatigue testing still uses ‘uniaxial loads’ (loading in one direction), although real components are exposed to ‘multiaxial loads’ (loading in multiple directions), which means new products will see enhanced optimised designs that will contribute to less waste. In terms of future developments, the project will also allow tackling the ‘enigma’ of experimentally reproducing, in a lab, 3D cyclic stresses that more accurately replicate what happens in real engineered components (figure 2). With new materials being developed every year, we believe ultrasonic fatigue testing will be the standard testing procedure in the future as it is estimated that it can lead to savings of between £13k and £71k per ASTM E379/ISO12107 material test programme.
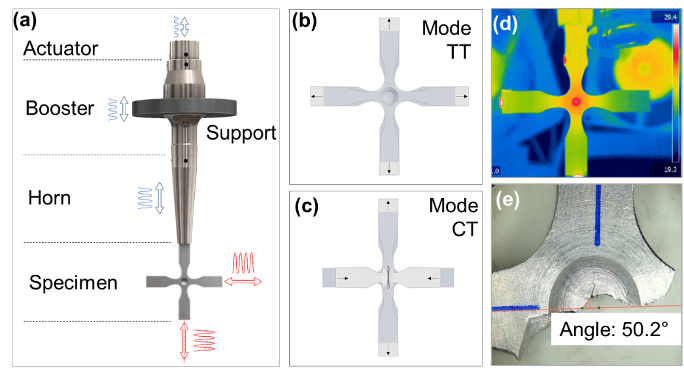
Figure 2. Multiaxial ultrasonic fatigue testing: (a) System; (b) equibiaxial specimen; (c) pure shear specimen; (d) thermographic image; (e) fatigue crack