Dr Sara Ashencaen Crabtree and Professor Jonathan Parker from the School of Health and Social Care discuss some of their recent research that explores the experiences of exchange students.
Although internationalisation is much wider in reach than student exchanges it is recognised that such exchanges can play a critical part in enhancing students’ appreciation and understanding of global issues. In this blog we describe some of our research exploring the experiences and perceptions of students undertaking an exchange and their ensuing culture shock. Accordingly, a three-year British Council PM1 2 funded research study into student mobility has provided a wealth of data on student learning in international social work placements; although this also provides some important implications for other types of international student exchanges.
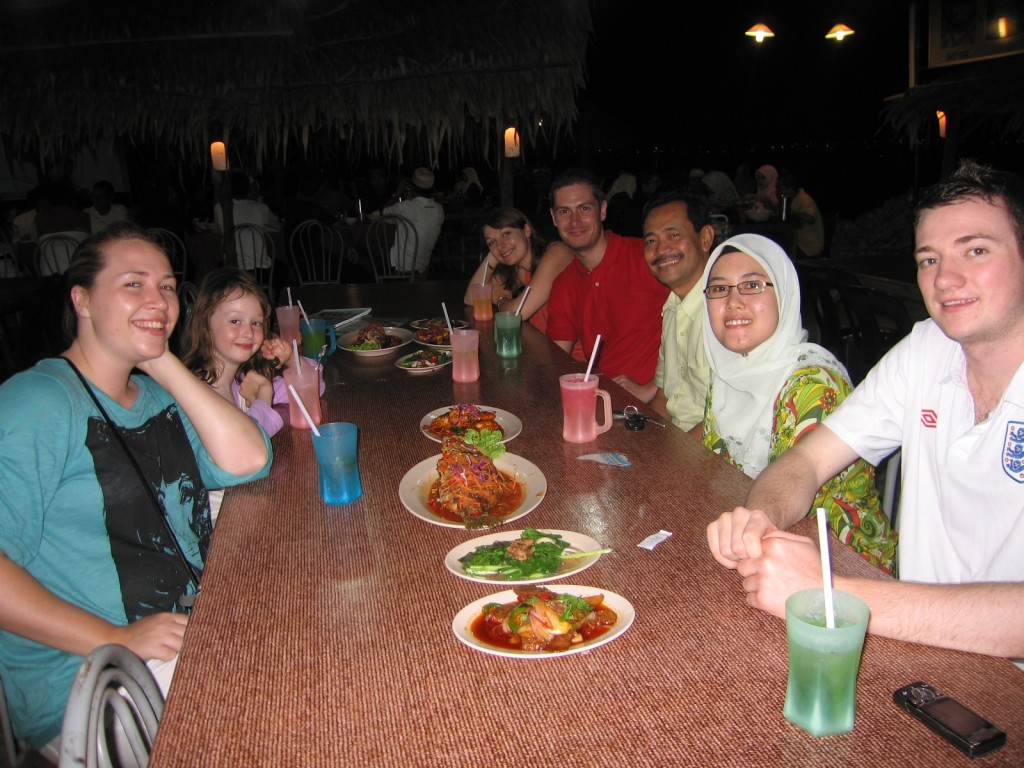
BU students at a dinner hosted by Universiti Sains Penang
In respect of these particular student opportunities, the sustainable development of the placements was created through the forging of Memoranda of Understanding with two participating universities: Universiti Malaysia Sarawak (UNIMAS) in East Malaysia; and Universiti Sains Malaysia (USM) in Penang. The history of the two universities differ; where like BU, UNIMAS is a new university, but with a lively social science faculty, which has been home to a thriving social work programme from the institution’s inception. USM, by contrast, is a long established, APEX status, research-intensive university, boasting the oldest academic social work provision in the country, and where social work programmes are offered at undergraduate, masters and doctoral level.
Consequently, BU social work students on international placements were able to benefit from an international support network of experienced academics working in concert for the duration of the placements, as well as receiving day-to-day support from local agency staff at the placement settings. The research element of the placements focused on the process of student learning in an unfamiliar cultural context, in which the writing of a daily log and a critical incident analysis formed the raw data collected by the students.
An analysis of data indicates that the concept of liminality – a process of moving through experiences from a status-less position to one of becoming – is useful in understanding the transitions experienced by the students and their confrontation with professional and personal values, often markedly different from their own. These are duly reflected on in terms of the mediation of the domains of familiar and unfamiliar ‘cultures’ and disciplinary practice. Liminality was also demonstrated by an awareness, new for some, of minority status and how this was perceived in the local context. Exposure to unfamiliar norms relating to gender, religion and culture, were also experienced, where, for example, previously unquestioned assumptions relating to Islam and women were re-examined upon encountering ‘strong’ Muslim feminists.
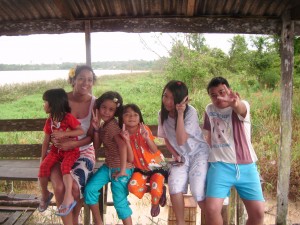
BU Student, Gatrine Muldoon, with the indigenous family who 'adopted' her.
Other aspects of liminality were constituted through the experience of encountering alternative ideological constructs, such as that of meritocracy as opposed to equal opportunities, ‘triage’ welfare provision as opposed to universal rights, or the strongly promoted Confucian values of family self-reliance wherever possible, even under the circumstances of absolute poverty. These experiences bring the students into sharp relief with their own, often, ethnocentric values, challenging notions of diversity, acceptance and cultural norms which, when worked through, can provide a depth of cultural sensitivity important in working in the contemporary global world.
While analysis of the data continues and the nexus of collaboration has widened over time to encompass other programmes in HSC, such as the new BA Sociology and Social Policy, dilemmas of how such partnerships may be fostered for mutual benefit in terms of expectation and reciprocation are raised. This has relevance for international partnerships between institutions where, for example, significant socio-economic differentials may exist, or where institutional research and resource capacity are unequal.
The outcome of this study, however, indicates a need to theorise teaching and learning in order to more comprehensively address global and internationalisation issues within and beyond the classroom setting. This also requires ways to address ethnocentricity effectively, so often implicit in the perspectives and assumptions of individuals, even those with insight into cultural relativity. Finally, the conclusion of this study will lead to practical outcomes in terms of follow-up research to examine whether international placements enhance employment opportunities for graduates.